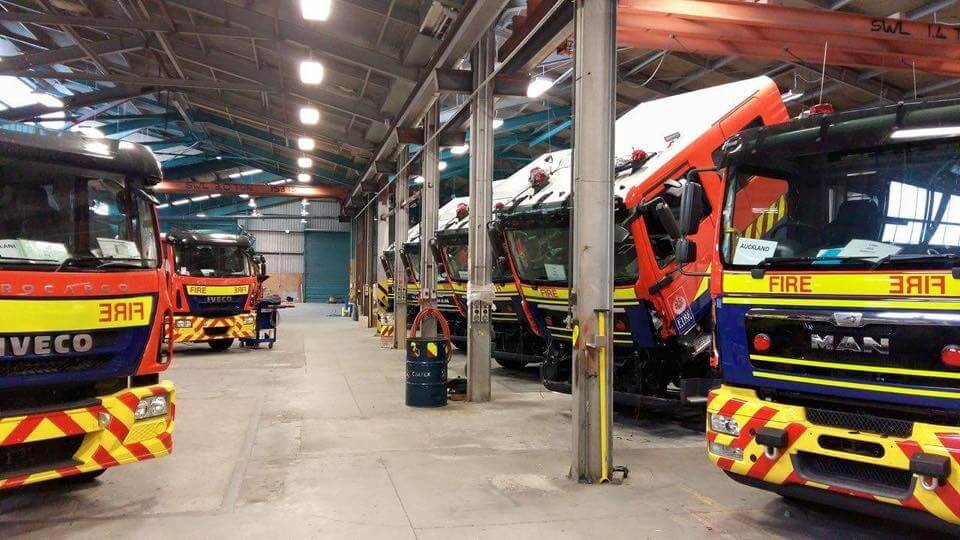
Members have continued to express their on-going frustrations with the Fraser-MAN pumping and pump-rescue appliances. At the recent Auckland Local Annual General Meeting, members directed the Secretary to publish a rebuttal to the propaganda originating from Fleet Management at NHQ. What follows below is correct to the best of the Local’s knowledge.
Background
The Project Team told the Union in Wellington back in July that they would only target the key issues identified, not improvements or the smaller problems, yet the 1st update states they're addressing all defects identified.
PTO Engagement Fault Affected by low voltages, ensure truck is plugged in on station - This doesn’t address when the appliance is off-station at events etc. where the truck is unable to be plugged in for long periods, nor when there is a prolonged power outage due to the Fire Service refusing to provide stations with emergency back-up generators. Given the draw on the appliance re: multiple radio chargers, TIC charger, Gas Detector charger, LMR and Merlin Boards, this was not particularly well thought out.
Fraser are trialling an alternative throttle with promising results - In stating the obvious, this should have been sorted prior to the rolling out of these vehicles, such as during the trial-that-never-was. This also suggests all the Fraser-MAN fleet are knowingly running around with defective throttles, begging the question, “Is this not a critical safety issue?”
Door Handles coming loose new part installed, it fixes all known issues - The Local contends that it does not. Wellington had major issues with 217 in the week following the 1st update and in Auckland there have been close to a dozen reported door issues on "fixed doors" in the last 6 weeks, including 251 having doors popping open.
Fixes completed on all 19: Door striker pins all reinstalled correctly - It seems Parnell have had further issues with this, to the point where the appliance has been removed from service.
The following are inaccuracies in the Q&A's released in conjunction with the 1st update.
What Process do we follow when buying appliances?
The second paragraph here states the project team includes frontline firefighters - This is incorrect: there was only ONE firefighter involved (from Christchurch), incidentally, who has zero truck, pump or fleet background. It also
mentions Union Representatives, yet only one Union Rep (other than the UFBA) was on the team (and not throughout the project, as he became disillusioned
when the decision to go with MAN was made by Mike Hall). It also has Area Managers involved on the project team - Why? They are not end-users and are
likely quite removed from their time operating or driving a pump.
The next paragraph states the RFT invites potential suppliers to meet the spec - MAN did not meet the spec in more than one criteria.
"Where tender responses do not meet a minimum level of acceptability against the spec, the price of those tender responses may never be seen by the project team" - How did the MAN meet the minimum acceptable level given all of the basic foundation problems (Chassis size, acceleration etc.)? This could only be possible if the specification was acutely flawed at the outset. Keep in mind that MAN has only provided what the Fire Service has asked for.
"In the case of the new Type 3, the highest rated cab chassis in terms of compliance with our spec was the MAN by a significant margin" - This is quite a statement when it is clear that it falls woefully short of the previous Scania cab/ chassis combination.
Who was in the MAN T3 project team?
Front line firefighters - As mentioned above, only one with zero fleet background.
Why did we move from Scania to MAN?
The MAN cab chassis rated the highest and that's why it was chosen - This was an exercise
completed on paper. Basic due diligence and a robust trial process would have involved actually trying different vehicles side by side, even if not
built up but with accurate loading weight attached to simulate and measure the built load.
Why didn't we build one appliance and take this around the country to see what crews thought?
We did do this to a certain extent - This
statement is rubbish. The Fraser-Scania rear-mount was a completely different vehicle. Different cab, chassis, different pump in a different location,
different locker configuration. It too was a Frankenstein monster, cobbled together out of the Fraser parts bin. This only tested the failed rear mounted
concept for a Type 3. The only aspect retained from that vehicle was the basis of the over-sized, inefficient body that is bolted onto the installed
subframe in an attempt to strengthen the under-rated MAN chassis.
We proceeded with tendering for an appliance with a configuration similar to the Scania Type 3's - The obvious response to this is, “How did we then wind up with something with so many flaws?” Different cab, chassis, powertrain, transmission, pump, locker section etc.
The first MAN Type 3 was operational in Wellington for some months before the subsequent appliances were introduced to service - Missing from this is the fact that the next 7 were already being built identical to the first. The commitment had already been made.
Given the relatively long period since the end of the previous Type 3 contract and the need to get older Type 3's out of the fleet, we opted to limit the trial period - There was no trial, period.
Why wasn't I consulted on the design of the appliance? Or my station consulted?
Instead we include firefighter representatives on the project team - As stated there was only one who has no truck, pump or fleet background. That worked out well.
Additionally we receive feedback on appliances over their lifetime. All of this feedback is considered when developing the specs for the new Type 3 appliance - This is not true. The Local is aware of member input regarding relevant points well prior to the first new-build Type-3 being completed, yet none of that appears to have been acted upon.
Feedback on fire appliances is always appreciated - This statement is missing the qualifier, “…only if it’s what we want to hear.”
Why didn't fleet visit the station, to measure the equipment, and then build the body to suit?
The appliance has been designed to accommodate the rescue trolleys that some stations use - This is another untrue statement. A rescue trolley was only accommodated after Auckland City refused to accept the Fraser-MAN unless the trolley was
provided for. The Union was told that this could not occur, as no other location in the country had trolleys and they did not fit with the Standard
Stowage matrix developed for this build. Wellington Central originally agreed to accept the first Fraser-MAN without a trolley, something that they
had in their previous P-Series Scania, with the proviso that it (the trolley) would be fitted at a later date. This assurance was not honoured, and
217 lost their rescue trolley. Auckland City would not be swayed from their position that a rescue trolley must be supplied before the new 207 could
be commissioned. Approximately $20,000 was spent modifying the appliance to allow this to occur.
Why is the new appliance 0.5m longer than the current Type 3? The body rear overhang was made longer to ensure feeder hose trays would be larger to accommodate six lengths of hose - This an odd statement. The old Series-3 and 4 Scania's, Mitsubishi's and Safety Cabs had shorter bodies yet carried 8 lengths of feeder. The P-Series Scania’s carry six lengths. If the above is the justification for the longer body, it sounds like a poor design. Additionally, our large urban centres are becoming tighter to manoeuvre through. A more intelligently designed compact appliance would have been a significant step forward.
Are the lockers larger than the Scania T3?
Yes. Scania is 5.76m3 whereas MAN is 6.36m3 - This fails to mention that
a lot of the additional space is unusable due to the flat-earth layout and the arrangement of the locker doors, with the roll being located at the
front of the aperture rather than at the rear. As well, the space behind the rear panel contains a wiring loom, is sealed off, and is unusable as locker
space.
Is there more room for the officers PPE in the front?
Yes. Extra space has been provided under the LMR MSU - That
space barely fits a bunker coat, not boots and over-trousers. This is inaccessible to the officer due to the layout of the binnacle containing the
LMR and control switches. In the Scania the bunker coat could be safely placed on the dash or centre console; the Fraser-MAN cannot accommodate this
due to the narrow dash and different centre console layout.
Where are we going to put the large airbags?
A deep shelf provided in the C Locker - Indeed, but not much space for
low pressure airbags. Perhaps there was a lack of awareness of those.
Why is the standpipe stowed in the locker rather than the back step?
To provide additional load security and help keep the standpipe clean - The Union is unaware of standpipes falling off the previous T3's with the mounting tube. Additionally, volunteer appliances still have standpipes mounted
externally. Since when have dirty standpipes actually been an issue? Anyone?
Also the standpipe is located in the same locker as the feeder hose that needs to be accessed to use the standpipe - Operationally, we use a standpipe at almost every call. We rarely use the feeder at most calls, and in the majority of the calls where it is used the go-to is the length of 90mm coiled. Operational input would have informed this.
Why is the gear selector located in the dash?
The gear selector was originally positioned near the park brake. It was shifted to the dash so the driver does not need to take their eyes completely off the road when changing gear - Genius,
lets locate a rotating type selector on the dash next to other rotating type selectors that control the heating and rubbish air conditioning. Drivers,
particularly at night, have turned on the heater a number of times instead of reversing. This is why T-bar gear selectors are better; you do not have
to look to change gears.
Why don't we have t-bar selectors?
It is becoming more common for trucks to have push button or rotary style gear selectors. The style of gear selector is not considered of great significance -…to those of us who sit in an office and determine what those who drive the appliances will prefer, without asking them. Awesome, although, it does matter to drivers. Blane and Moran’s extensive operational background has obviously allowed them to figure this out. Although,
if they actually consulted they would know the issue of rotary selectors on the early 3-Series Scania’s.
If it's better, how can it be cheaper?
When we say better, we mean a better alignment with the NZFS technical requirements. A chassis can be more expensive if it is designed to carry a far greater weight than required - Totally
disagree that these vehicles are better. This cab chassis has proven numerous times and in numerous ways to be inferior to the previous P-Series Scania.
That last sentence in bold italics completely sums up the terminal Achilles-heel in these vehicles. They have been designed to fail, not by intent,
but, as an accumulation of the whole. This is the net effect.
A proper trial involving a few prototypes would likely have avoided the current situation, a situation where $20 million of levy payers’ money has been wasted on a fleet of lemons with irretrievably bad DNA. A situation where vehicles less than six months old are literally coming apart at the seams (Christchurch). Where vehicles have had their wiring interfered with to the point where they won’t start when called upon to respond. Where pumps will not go into gear or drop out, where throttles do not engage or cease working, where doors pop open at random and inopportune moments.
Consider that last point: who would be responsible if a door randomly opened when a vehicle was passing a group of cyclists or attempting to negotiate lanes on a crowded motorway, causing an injury or serious injury accident? It won’t be fleet, it won’t be the Officer in Charge, and it won’t be the Area Manager. It will be YOU, if you are the driver.
In summary:
- The Fire Service has finally admitted there is a problem with these vehicles after spending the better part of a year ignoring their front-line staff.
- Blame is being apportioned on MAN and Fraser Engineering, with Fraser coming in for the bulk of the criticism. The Fire Service is conveniently ignoring their own culpability in failing to provide oversight or run a thorough and rigorous trial.
- A testing regime is being worked on to put the vehicles through in order to ensure that they are fit for service, which is a genuine cart-before-the-horse situation.
- Millions of dollars is being spent to correct a number of faults, some of which may be impossible to solve due to the flawed DNA of these vehicles
- 47 vehicles have been ordered, of which 19 are in service but 3 are Blacked. More are being completed on a weekly basis.
- The Union is represented on the Project Team by President Peter Nicolle. Admittedly, this would not have been the Local’s first choice for this role, however, Peter was appointed by the Union Executive to fulfil this role and he has been consulting with the Locals on their particular concerns. Peter has given an assurance, and his actions are bearing this out, that we will have a voice as this project goes forward.
- The Local has endorsed a proposal to re-assign the Fraser-MAN appliances to stations and Brigades that are less-frequently called out in order to prolong the vehicles’ “lives” and place them where they will be most useful.
The Local reiterates the importance of logging all faults and failures as well as reporting them as near-miss events in order to ensure an accurate record is kept on the infirmities of these appliances. If an appliance, (any appliance), is deemed to represent a safety risk, then it needs to be parked until such time as it can be repaired and verified as being safe and fit for purpose.